Detector Mechanics and R&D
The high-luminosity upgrade of the CMS detector
The LHC complex will undergo a series of upgrades (High Luminosity Phase of the LHC, HL-LHC) in order to increase the instantenous luminosity to unprecedented values at hadron colliders. The HL-LHC is expected to be ready for data taking in the 2020s with significant detector R&D already taking place now. The focus of the Jung group is on the instrumentation of the innermost region of the CMS tracking devices using silicon detectors. The Purdue Silicon Detector Lab is a state-of-the-art in-house facility for broad R&D aspects and assembly of silicon detectors for the HL-LHC.
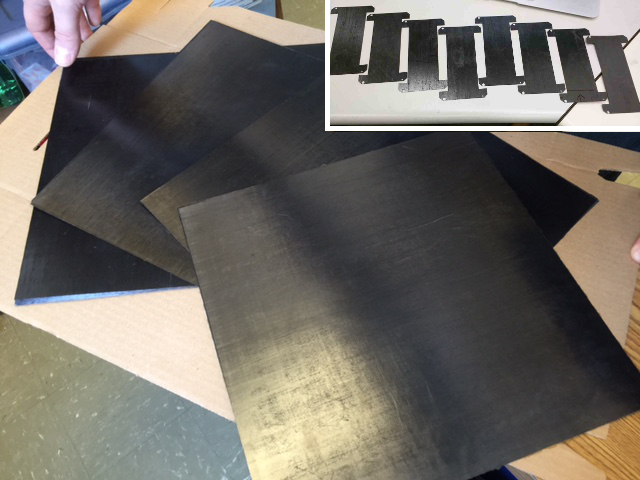
Figure 1: Custom made sheets of individual
layers of 60 micron thick carbon fiber plys
employed as baseplates of the support
structures of silicon detectors.
The precise track information is the basis for the identification of particle jets originating from b-quarks, which is one of the most efficient methods to enhance H→bb decays, top quark decays and a large amount of beyond the standard model signatures. A silicon detector provides the precise track reconstruction required to perform this identification. Non-active materials (support, cooling, electronics) in a silicon detector degrade the performance of the track reconstruction of charged particles going through the silicon detectors. Hence, the R&D focus is on light-weight materials and their use for support structures of silicon detectors. In particular carbon fiber is at the center of the ongoing R&D activities, since it is light-weight and mechanically very strong.
Other examples being custom made carbon fiber sheets using an in-house facility, see Figure 1. These sheets are used to build mock-up silicon detector modules which are as close as possible to the real detector modules also using raw silicon. The mock-ups are employed to study and test the thermal performance under real conditions. The collected data is analyzed and compared to resuls of a finite element analysis of the expected heat distribution. Figure 2 shows an example of a mock-up already equipped with temperature sensors. Jung’s group is doing R&D for future detectors, namely support structures for large future circular collider (FCC-ee, FCC-hh), muon collider and other future machines. The Jung group has submitted a white paper on future detector mechanics to the snowmass process and it is included in the WG report on solid state detectors.
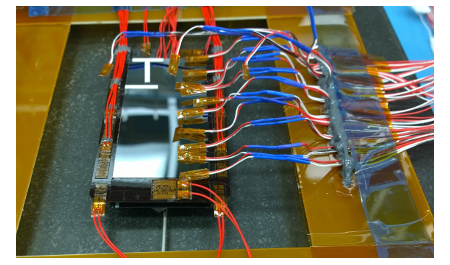
Figure 2: Preparing a silicon detector mock-up
for thermal measurements using parts and
pieces of real silicon detectors.
Jung is an affiliated member of the Purdue Composite Manufacturing and Simulation Center and utilizes the facility to develop a variety of carbon fiber based superstructures supporting the entire inner silicon pixel detector. The total length of the cylindric superstructures is about 5.4m, composed of 4 half-cylinders each with about 2.7m length and additional larger tubes ranging in size between 0.5 to more than 2m. A first prototype of a shorter section ("step section") of the half-cylinders has been manufactured in February 2018 at the CMSC employing a 3D printed mold used to cure a layup of Carbon Fiber prepreg. Figure 3 shows the 3D printing process of the mold, which is then later used for the layup of the Carbon Fiber layup (top small insert), and the bottom insert shows a laser scan of the "step section" prototype.
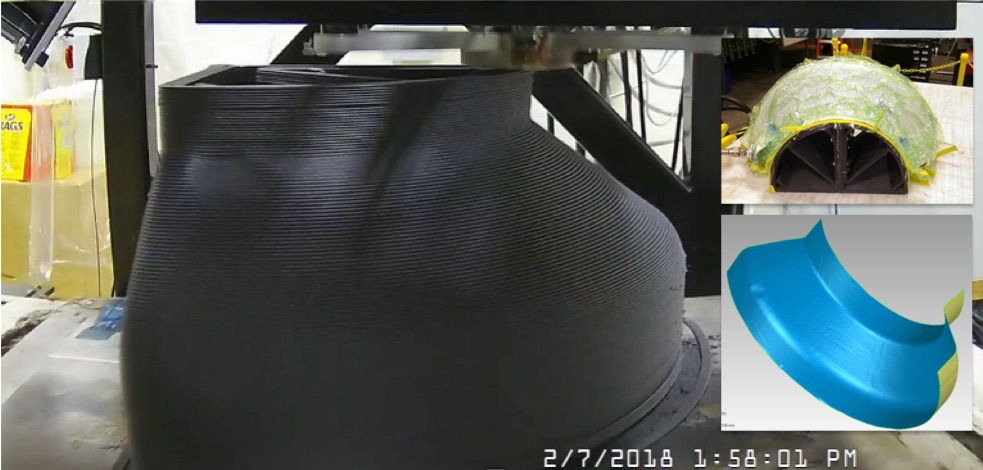
Figure 3: 3D printed mold and final cured
Carbon Fiber layup for a section of the large
supporting superstructure of the new CMS
phase II silicon pixel detector.
Most recently, Purdue researchers in the Purdue Silicon Detector Lab (PSDL) and the Composite Manufacturing & Simulation Center (CMSC) have worked together on the challenge of removing 35kW of heat relying on lightweight composite tracker support structures. They have been creating prototype cylinders made of carbon fiber composites and have now officially created a working prototype that will be installed and tested at CERN near the end of 2022. Purdue CMS scientists currently work on more testing, metrology, loading scenarios, and once completed prepare the eventual shipment to CERN for more tests. Once the BTST prototype arrives at CERN and has been tested, the Purdue CMS team will work on design and manufacturing of the final full-length, 5.3m (16.4ft), structure between 2022-2023. This build will rely on an external fabrication partner given the enormous size of the structure. Figure 4 shows the first prototype with full diameter but shorter length of about 1m, which was received in November 2021.
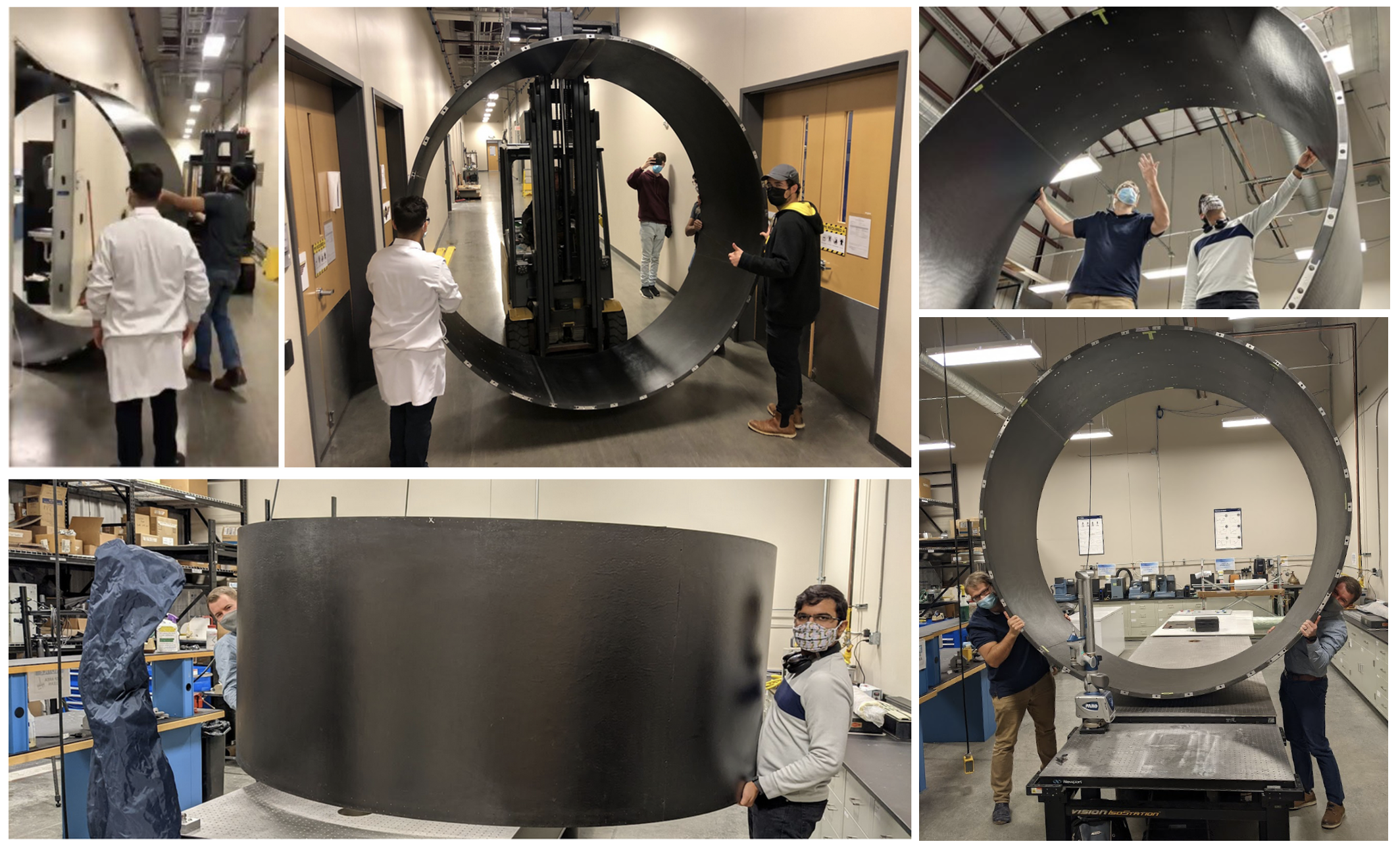
Figure 4: The large BTST prototype, measuring roughly eight feet across, barely fit through the doors of the lab at CMSC.
The Jung group is commissioning a cooling test stand employing liquid CO2 as coolant at the Purdue Silicon Detector Lab to facilitate local thermal tests of the mock-up modules build in house. Please take a look at the Open Positions/Contact page for Ph.D. and undergraduate research opportunities related to Detector R&D in the group. Undergraduate researchers are an integral and critical part of the research effort.
Detector R&D
The Jung group is engaged in Detector R&D for future detectors in high energy physics, e.g. Muon Collider, Elektron-Positron Collider or a Future Circular Collider (ee/hh/ep). Undergraduate researchers are an integral and critical part of the research effort.
We are very happy to have been awarded by DOE for R&D on the development of Detector mechanics of future tracking and calorimeter devices.
- Low-mass support structures with integrated services for silicon detector systems - The Jung group joins forces with CMSC's Eduardo Vaca to utilize transformational techniques and approaches to design and manufacturing low-mass support structures with integrated services. We study solutions towards integrated cooling channels and light-weight mechanical support structures that are optimized for thermal performance and low radiation length.
To understand the bottlenecks in material choices, we have studied the thermal performance of a hypothetical support structure inspired by the CMS Inner Tracker dee support structures. A schematic (half) multi-layer ``stack" of materials is sketched in Figure 5, with the cooling pipe at the bottom and the silicon device at the top. Figure 6 shows the temperature difference of the silicon chip with respect to coolant temperature as a function of the thermal conductivity of the various material layers. The shaded bands for the TIM layer and epoxy layer around the cooling pipe are determined by varying the nominal thickness of these layers by given amounts.
Figure 5: Schematic view of the cross-section of a representative multi-layer support structure inspired by the CMS Inner Tracker dee structure.
Figure 6: The temperature difference between the hottest point on the chip and the coolant as a function of the thermal conductivities of different layers of a hypothetical support structure shown in Figure 5. More details in the text. - CalVision project, titled “Maximum Information Calorimetry", where we are working towards the development of a basic thin walled small-square honeycomb structure resembling a future calorimeter cell. Such a structure utlizes light-weight composite support structure materials and should be able to support a realistic calorimeter.
Latest News
- Latest CMS News
- Observation of tt Entanglement
- DOE CMS upgrade award
- AirForce Phase III award
- DOE awards AI grant
- CMS Gold award
- Enormous Carbon Fiber prototype
- CMS upgrades funded
- Ramdas Award 2019
- New physics ?
- Summer 2018 UG exchange
- CMS phase II pixel upgrade workshop @Purdue
- Huffington Post: A new inner detector installed for CERN CMS experiment
- All News