|
Search Engines and Directory: |
|
|
To pattern a substrate with nanometer-scale
objects, a versatile printing technology must be developed.
In what follows, we borrow heavily from the extensive published
literature on the subject of micro-contact printing. Before
printing can occur, the substrate, stamp and “ink”
must all be fully prepared for the procedures. This is an extended
process of cleaning and drying, of diluting and mixing. All
the proper steps must be taken for each successive experiment
to ensure intelligible results. We describe below some of the
techniques we have developed to pattern proteins onto substrates.
First, the substrate must be cleaned. Typical glass slides (Gold
Seal, Hungary) are used in these experiments for their cost-effectiveness,
transparency and their quality of being a good material on which
to deposit proteins. The substrates are cleaned with solvents,
acetone and methanol, then placed in sulfochromic acid for 45
minutes, followed by rigorous rinsing in distilled water. The
substrates are then silanized over night in a solution of chlorodimethyloctadecysilane
(0.02 M) in an anhydrous toluene solution. [6] Next, the substrates
are removed from the silanization solution and rinsed in toluene
solution, followed by sonication in methanol. The substrates
are then left to dry
in an oven for 30 minutes. After the preparation
is complete, the substrates are kept in a closed vacuum container
to avoid dust exposure. Once the glass substrates have been
prepared, the stamps themselves must also be cleaned and primed
for the experiment. All stamps are made of poly(dimethylsiloxane)
(PDMS). They are fabricated by casting and curing an elastomeric
polymer, Sylgard 184 (Dow Corning, Midland, MI), against a photoresist
micropatterned silicone master. [6] The process can be visualized
in figure 1. The master relief pattern is a negative relief
of the stamp. The PDMS stamps were cured for two days at room
temperature, then sonicated in a solution of ethanol and water
(1:2 mixture) after being cut into the desired size. Once the
cleaning has been completed, the stamp is then oxidized using
a plasma cleaner.
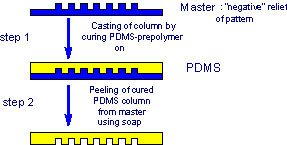
Figure 1: Process of creating PDMS stamps from silicone Master.
The oxidized stamp is then coated with the appropriate
antibody. To coat the PDMS stamp, an antibody solution is mixed
with a concentration of 200 ?g of either bacteria or protein—dependent
upon the experiment—diluted in one milliliter of phosphate-buffer
saline (PBS). Once created, the antibody solution is used to
coat the PDMS stamp over a period of 20 minutes. After 20 minutes,
the excess is drained off the PDMS by dripping onto an Accuwipe,
and the PDMS stamp is dried with a stream of nitrogen. Then,
the PDMS stamp is applied to the glass slide, first by placing
the stamp onto the slide followed by the application of a firm
pressure by pressing down lightly onto the stamp with a finger.
As the antibodies come into contact with the glass surface,
they bind with the chemistry on the surface, uniformly transferring
themselves from the PDMS stamp to the glass substrate as shown
in Figure 2. Thus, a periodic array of antibody squares is created
on a substrate.
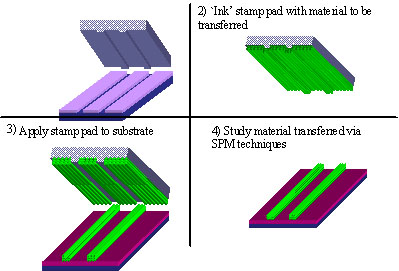
Figure 2: Process of printing antibody in a micro
array
|